Current Status
Not Enrolled
Enroll in this course to get access
Price
$139.00
Get Started
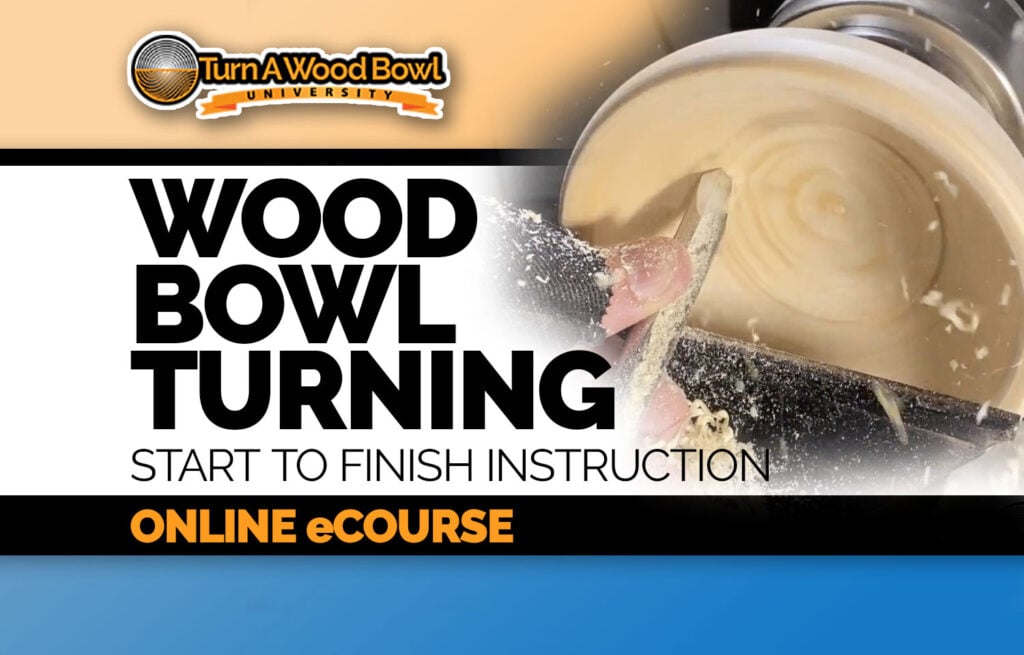
Course Content
03 Safety
You don't currently have access to this content
04 Equipment
You don't currently have access to this content
05 Bowl Blank Preparation
You don't currently have access to this content
06 Mounting Bowl Blank to Lathe
You don't currently have access to this content
07 Understanding Lathe Speed
You don't currently have access to this content
08 Tool Rest Basics
You don't currently have access to this content
09 Bowl Gouge Sharpening Basics
You don't currently have access to this content
10 Bowl Gouge Push Cut
You don't currently have access to this content
11 Creating a Mortise Recess
You don't currently have access to this content
12 Tenon Shaping
You don't currently have access to this content
13 Understanding Grain Supported Cuts
You don't currently have access to this content
14 Preventing Bowl Gouge Catches
You don't currently have access to this content
15 Bowl Gouge Curved Cutting Passes
You don't currently have access to this content
16 Riding the Bevel
You don't currently have access to this content
17 Four Bowl Gouge Cuts
You don't currently have access to this content
18 Shaping Bowl Exterior
You don't currently have access to this content
19 Reversing Bowl in Chuck
You don't currently have access to this content
20 Shape Bowl Rim
You don't currently have access to this content
Hello,
I follow your YouTube videos and I am enjoying your beginner course so far with one exception. Please don’t allow ads on the webpages for a course. Obviously its not what anyone wants to see. Regardless I am enjoying it and plan on purchasing more courses in the future. Thank you.
Regards.
Tom,
Thank you for writing and sharing! I’m sorry for any inconvenience.
Consider using an ad-blocking browser like Brave. I think you’ll enjoy the experience.
All the best to you and Happy Turning!
Kent
Hey Kent. I’m not sure how the access side of things works for your online video courses. I don’t have any wifi/internet connection in my workshop but would ideally like to be able to pause what I am doing at the lathe and then view video content on my iPad rather than having to walk back to the house every time I want to review something in the video again. Does your course delivery solution allow for offline viewing?
Ade,
Thank you for writing and sharing! Unfortunately, you will need an internet connection.
Here’s a possibility – use your phone’s wifi hotspot setting to connect your ipad in your shop. Setup the hotspot on your smart phone and then link the ipad wifi setting to the phone. Let me know if that works for you.
All the best to you and Happy Turning!
Kent
Hi Kent – Well I just finished the last of your four courses and like so many others, want to thank you for both the courses as well as your amazing YouTube content. I wonder at times if you were an expert woodturner that became a great teacher, or the other way around? No need to answer 🙂. I am especially impressed by your ability to create content bearing in mind the challenges/questions/struggles we all face as we learn. Thank you!
John,
Thank you, for the kind words! I’m glad you’ve enjoyed the courses. Please consider leaving reviews on the sales page of each course here > https://turnawoodbowl.com/shop/
As for the teacher/woodturner, actually I’m a graphic designer/photographer who learned woodturning and saw where many fellow turnings were having issues. I built the website first and then did YouTube videos. It’s funny how things happen. Again, Thank you for your support and I’m thrilled you have benefited from the course.
All the best to you and Happy Turning!
Kent
These courses have been great for helping me get started. A couple questions:
1. Do you always work from one side of the lathe or do you ever cross over to the opposite side for some cuts?
2. Do you have a recommendation for an oil or other finish that will give a high gloss luster?
Thanks’, Greg
Greg,
Thank you for writing and sharing! Good questions.
1) I don’t cross over to the other side because the lathe rotation needs to be coming towards us while we turn. Also, the threaded devices, like the faceplate, stay in place with this over-the-top rotation. If turning the opposite direction, they would unscrew.
2) Here’s what I do for finishes and how I decide. https://youtu.be/ZozfMGphLUM?si=1tLzEjoJb62ugyQm
All the best to you and Happy Turning!
Kent
Kent
I have learned a great deal from your course and your videos! Thank you for your diligence in methods and instruction. I have been turning for a year now, after getting over some nasty catches that almost stopped me. But I am learning and loving the creation and discovery that comes from opening a bowl up from a hunk of wood! Fantastic.
I have a question about gloves. Because of my nasty catches I like wearing a tight glove with ballistic sort of patch on the fingers! But most resources so NO. But I see you usually wear one. Can you shed light on this from you perspective?
James
James,
Thank you for writing and sharing! I’m thrilled to hear you are benefiting from this course.
As for the glove, please see this video > https://youtu.be/FByeN7oOJPs?si=I4TKiG6SI4rhuAH0
Happy Turning!
Kent
PS – Please consider sharing your feedback about this course on this page > https://turnawoodbowl.com/product/tool-sharpening-for-wood-bowl-turning-online-course/
Kent, I am looking forward to taking this course, having already watched a lot of your YT videos (some twice). Just based on those videos, I turned my first bowl today from a spalted ash blank with only a 5/8″ bowl gouge. I was impatient to finish, so I didn’t get the walls perfectly uniform and there was some tearout on the inside (closed rim) wall, but it came out very well. You are an amazing teacher and I am very grateful. All the best, Paul
Thank you for the kind words, Paul. That first bowl is super exciting isn’t it!!! Save it forever.
All the best to you and Happy Turning!
Kent
I was wondering what kind of band saw do you have?
It is a 17″, 2hp, Grizzly with foot brake. Happy Turning! 😉
Hi Kent. Hope all is well. Firstly let me say how much I’m enjoying the course work that you created. Im thinking about upgrading my lath and would appreciate your professional opinion. I currently have a small pen turning lathe and I want to upgrade to either a Jet 16-40 or Laguna 18-36. The problem is that I don’t have 220 power available so I’m looking at the 115 volt models. Before I make this large purchase can you help me to understand the difference between 220 and 115 volt models. Does the 220 deliver more power or torque and will I be disappointed with the 115 volt unit. Thanks in advance for your response.
Thomas,
Thank you for writing and sharing! Great question.
Yes, you are right about the extra power and torque with a 220 motor. And if you plan to turn bowls of a useable size, you will definitely benefit from that power. It’s common for 110 or 115v motors to bog down when turning larger bowls.
I suggest contacting a few electricians to get an idea of what might be done. I had the same thoughts you are having and it turned out the electricians could run a line off our existing dryer circuit with very little trouble. I now run my lathe and bandsaw on 220. Also, get several estimates. I’ve found large swings in prices from various electricians.
All the best to you and Happy Turning!
Kent
I’ve taken all 4 of your courses, awesome job, extremely helpful for me to improve my bowl turning technique. I recently have turned green wood, Madrone and Arizona Cypress. After the wood was rough turned, dried and then returned to complete the bowl, I have some difficulty in trying to re-balance the bowls. I re-mount the bowls on the head stock, 4 jaw chuck, tenon, tail stock up and holding the inside of the bowl. I start on the rim, then the exterior and finally the interior to balance and complete the bowl. Some of the bowls are more than 3/8″ out of balance to start with. I use a 5/8″ or 1/2″ bowl gouge with 55 degree bevel. I have a very hard time trying to re-turn the exterior to balance it. Is there a proper sequence to follow as where to start on the bowl, tool, lathe speed, shear cut versus scrape cut to basic old, try to ride the bevel cut and a lot of down pressure on the gouge on the tool rest and slow, shaving cuts.
Clark,
Thank you for writing and sharing! Great question.
A couple things could be happening.
1) Making the tenon super clean and crisp is very important for remounting or reversing the bowl and having it turn true. If it is off just a touch, loosen the chuck and rotate the bowl a touch and re-tighten. Then see if it turns more true. Usually this will yield good results.
2) If you are turning a blank with any moisture, which almost all blanks have, and you are waiting for any length of time to turn the bowl around, the tenon might be warping or distorting. Do the full turning all at one time. Do not delay turning the interior after turning the exterior. A little story – I turned once a week with a group of other turners. Some turners would start the exterior of a bowl one week and return the following week to pick up where they left off. Inevitably, they would struggle with the tenon not seating well and huge wobbles in their pieces. They spent more time trying to fix the week long distortions and cracks that were created vs. just turning the complete bowl in one “sitting.”
I’m guessing that one of those answers might help. Please let me know.
All the best to you and Happy Turning!
Kent
I just bought my first lathe and turned 4 pens that came out pretty nice. I just tried my first bowl and let’s just say I have a lot to learn. Feel like I might as well have used a weed whacker instead of a gouge. Is there anywhere to take a hands on class?
Adam,
Thank you for writing and sharing! I’m sorry you’re having troubles. I would suggest checking out the Bowl Gouge Mastery and Tool Sharpening courses http://www.TurnAWoodBowl.com/shop I will guide you through everything you need to know and you can come back to the video lessons anytime you need them.
All the best to you and Happy Turning!
Kent
Kent,
I am new to turning (about 2 years now) and find your YouTube videos to be extremely helpful and detailed. The multitude of different videos has helped to hone my skills on the lathe and nearly eliminate the ever frightening catches. I decided it was time to invest in your sharpening and wood bowl courses to get down to the detail level. Best investment I ever made! Appreciate your patience and thorough explanation as each lesson is thoughtfully explained and demonstrated. One area that I have struggled with is the interior clean out and maintaining a consistent wall thickness. I have watched lesson 21 multiple times and learn something new every time! One thing I have found useful for my particular set up is to turn the lathe in reverse and make cuts from the right side of the bowl. It allows me to have a better line of sight and control of the wall thickness. I have seen very little on YouTube about this method. Is this something you use or would recommend?
Thank you for writing and sharing! Good question. I don’t typically turn across the lathe in reverse, but it is an option.
Be sure you have turned for awhile in forward and the chuck or faceplate is firmly seated on the headstock. If you get a catch or if the chuck loosens in reverse, the chuck and bowl will come shooting off the lathe. If your chuck or faceplate has a set screw on the headstock, be sure to lock it down first.
I say if the process works for you keep it up!
All the best to you and Happy Turning!
Kent
Hi Kent.
I just completed the tree to bowl and the bowl turning courses. You get a standing ovation as an instructor! In the past, I worked as an instructor for chiropractic interns at a chiropractic college. I know good instruction when I experience it.
My question for you is would the sharpening course be worth it to me if I have a Tormek system with all of the jigs? I gathered that you mainly cover two other systems. If there is enough theory in the course that you think I would benefit from it, I’ll do it. The other two courses were great and I’m having a blast turning.
Thanks,
Brian J. Huth, D.C.
Brian,
Thank you for your kind words. I’m thrilled you have enjoyed this course.
As for the Tool Sharpening course, while we do not cover the specifics of the Tormek system, we do cover many aspects of shaping and sharpening that are rarely covered elsewhere. These universal concepts and ideas can easily be adapted and will benefit anyone sharpening on any system.
All the best to you and Happy Turning!
Hi Kent: I am on the lesson where we clean out the inside of the bowl. Sometimes the gouge comes across nicely and other times it jumps about on and off the tool rest. I am trying to follow the bevel but it still jumps around. I have looked at the height of the tool rest as well but it seems I cannot get it right consistently. Any ideas on what I need to do here?
Daniel,
Good question. It could be a couple of different things.
First, try dropping the handle a bit during the cut and then returning to the center bottom point. If you were to draw a line from the beginning of the cut at the rim down to the bottom, the line would be a smooth hill. As you start the cut, you climb the hill and then come down the hill at the center. This curved cutting path, compared to a straight cutting path give the tool bevel more contact area.
Depending on the size of your bowl and the size of the gouge, the gouge heel might be rubbing. If the bowl is small and the gouge is larger than 3/8″, you might want to grind back the heel so the tip of the gouge has more room to rotate within the cutting path. I illustrate that in this video https://youtu.be/t6LOqcngeOM?t=893
Try addressing this two issues and let’s see if that relieves the problem.
All the best to you and Happy Turning!
Kent
Hi Kent, approx how long is the course time wise? Cheers
Hayden,
The videos alone are almost four hours of content. There is much more material as well.
All the best to you and Happy Turning!
Kent
Thanks for the course Kent. I’ve been turning pens for 10 years and had only turned a couple of small chalices before trying to imitate what I had watched on YouTube. I saw several people making beautiful walnut bowls and tried it myself. Luckily no serious injuries. I thought about making a YouTube video myself of what not to do.
I was delighted to find, purchase and follow your course. I systematically followed your demonstrations and instructions. You are an excellent teacher. I am happily continuing to learn and getting better with each bowl. As I attempted to make each bowl, being able to go back and watch lessons over and over again has been essential for me. I was able to notice the angle of the chisel and correct mistakes I was making. I had to use my imagination to determine your body positions. Anyway, this training was worth every penny.
I especially appreciate the safety instructions you were very careful to include.
Thanks, Carlin
Carlin,
Thank you for the kind words. I am so glad you have found this course beneficial.
It sounds like you are going about it the right way, learning one bowl at a time.
I wish you all the best and Happy Turning!
Kent
Kent, I have learned a lot from your turn a bowl ecourse and videos. I have a Jet 1236 lathe and want to make or purchase a tailstock shaft extender. I have an extra shaft and bolt.
Thanks for your great support.
Mike Runyan
Kent, I discovered a extension on Amazon . I scored several walnut, cedar and camphor logs and I followed your guides for making green bowls. Using a small microwave and wood chips seems to really speed up the drying process.
Thanks again.
Mike
Mike,
It sounds like you have a good system going. Enjoy and Happy Turning!
Kent
Mike,
Thank you for writing and sharing! Here’s a link for you https://amzn.to/3PEJmED
All the best to you and Happy Turning!
Kent
Hello Kent:
I am at the stage of turning the bowls around and taking out the inside of the bowls, and am having trouble. As soon as I start with my bowl gouge, the bowl flies off the lathe, leaving about half of the foot in the grip of the lathe. This has happened once with a 1/2 ” gouge with a fingernail grind, and once with a 3/8 ” gouge with a 55 degree grind with the swept back wings you use. Is this a frequent result when using pine, or am I doing something systematically wrong? Thanks for your help.
Tom K
Tom,
OK, not to worry. It is most likely one of two issues or possible a combination of the two.
The wood could be super dry and brittle. If it is, then apply some super thin CA glue to the base of the tenon as soon as you make the tenon. It will soak in and saturate the grain around the base of the tenon. Let it dry and then lightly recut and “sharpen up” the tenon shape. you don’t want any CA blobs preventing the tenon from seating in the chuck.
Another issue could be making too aggressive of a cut when turning. You should only be slicing away a very thin shaving with the corner of the bowl gouge. Be sure the tip of the gouge is rotated almost 45° in the direction of your cut. You can also lower the handle of the gouge a few degrees to reduce the direct tool impact further. Just be sure each pass is only shaving a thin layer each time. If you are seeing thick shavings that look like ground hamburger you might be getting too aggressive with your cuts. You want to see thin whisps of shavings instead.
Let me know if these tips help.
All the best to you and Happy Turning!
Kent
I have watched almost every one of your videos and am a huge fan! Although this course was a refresher from what you have on your channel I did benefit in 3 ways by taking the course
1 every thing that you teach is all in one place.
2 I can take a refresher in a technique from 1
source with out having to search and watch
several videos
3 the 2×6 construction grade blanks are a great
way to reinforce basic skills that can be
practiced at a reduced cost.
Al,
I’m so glad you are enjoying the course. Thanks for joining!
All the best to you and Happy Turning!
Kent
How would I go about lowering the RPM of a Lathe motor from a range of 600 to 2400 RPM, to a lower range of 300?
This motor is 2 HP, 110v, Single Phase, 14 A. And if there is a way to do this, would there be any torque be lost?
Steve,
Great question.
I don’t know the specifics, but I believe it involves adding a switch (perhaps a 3-phase) switch to the motor that will allow variable control.
My guess is you could talk with someone who knows electricity and small motors and they will be able to help.
All the best to you and Happy Turning!
Kent
Hello
I’m thinking of gifting a course to my partner. I am having trouble deciding. Can you tell me if the concepts of Tree to bowl are covered in the Start to Finish course? Also are the prices in USD. We are in Australia.
Regards
Sylvia
Sylvia,
Great questions.
The two courses are completely different. Tree to Bowl covers how to collect, process, and prepare raw wood to be turned, but not turning itself. The Bowl Turning course covers all the steps from start to finish how to turn and complete a wood turned bowl, but does not cover preparing raw wood. However, in the turning course we use a simple, relatively inexpensive wood source for bowl blanks to turn.
If you’d like to gift a course(s) simply sign up and then email me (info@TurnAWoodBowl.com) afterward and I can readjust the login user name and password to the person you are gifting.
Thank you and Happy Turning!
Kent
Hi Kent:
While I was making the 2×6 blanks for the course, I glued up some 2x10s for additional practice, and I am having a problem. I am using a 5/8″ bowl gouge sharpened at 60degrees, and can start the cut nicely. But when I get about half way through the cut, the tool starts chatttering. I have watched the “Ride the Bevel” video, and I think I am doing things properly, but the results say otherwise. What part of my technique is going bad.
Thanks for your help.
Tom K
Tom,
If you are getting chattering, be sure you are not reaching too far over the tool rest with the gouge. You may need to stop and adjust the tool rest so it’s closer to the cutting surface.
Also, consider using a thicker gouge. If you are using a 1/2″ gouge, step up tp a 5/8″ gouge which will be more stable. See if that helps.
Happy Turning!
Kent
Are finished wood turned bowls safe for food, i.e. bread dough?
thank you.
Absolutely! There are some studies that suggest raw wood has anti-bacterial properties as well. Be sure to use a good food safe finish too. See this article https://turnawoodbowl.com/my-favorite-food-safe-wood-finish-waterproof-almost/
Happy Turning!
Kent,
I’ve been impressed with your teaching style and method. I’m about to sign up for the course. Before I do, I want to ask two key questions. First, with this being a hobby and my career taking 60+ a week, I’ll need to go slow. Is there any expiration date for the course? And second, once complete, will I be able to refer back to the course to relearn? thanks, Gary
Gary,
Thanks for writing.
Life-time access for all the courses.
You can come back anytime you like.
And FYI, if your week is busy, I suggest scheduling on 4-6hr session per week. This is how I learned. What is nice about this approach is you will build anticipation for that scheduled time. And you will have time to reflect on what you did afterward and how you can improve the following week. The best part is you will not burn out easily. Just an idea. Do what works for you. All the best to you and Happy Turning!
Thank you, Kent, for a valuable course! It has given me a lot of confidence and I’ll continue practising.
Christa.
You are very welcome Christa! I’m so glad it has helped you!
All the best to you and Happy Turning!
Kent
Hi Kent,
What I’ve learned. You can’t turn a quality wood bowl without sharp gouges. You can’t have sharp gouges without shaping them first. You can’t shape without an accurate depth gauge.
I made my depth gauge using the plans I purchased from your shop. I’ve shaped and sharpened my gouges. Now I’m ready to apply all of the content of this course to turning bowls. I highly recommend your sharpening course as a precursor to turning, and that’s what I tell my friends.
Thanks for all of the valuable information. Your courses are worth every penny.
Deba
Thank you so kindly, Deba! I’m so happy to hear you are benefiting from the course!
All the best to you and Happy Turning!
Hello and thank you so much for your videos on youtube and for offering an e coarse. A little bit about myself. My experience turning was one bowl in high school, but I loved it. I always wanted to do more, but could not justify the cost of a hobby. Fast forward to me turning 49 and still having that same passion, but again “I can’t spend money like that for just a hobby”. I had been feeling very sick for almost 7 months and went to my doctor. The year and a half after that doctor visit… well no way to fast forward through that. I am now 52 and cancer-free!!!! I took out a loan to celebrate and yes I after research, I bought a jet 1220vs lathe and all the chucks and tools listed in your videos and others. I live in South Dakota and the nearest club to learn in person is 4 hours away and not possible, also I learn better in person as someone can say ok here is why that catch or flying blank happened. My lathe has not been turned on for over 6 months because of this. When I said I took out a loan and bought things, I also bought the wolverine sharpening tool and the sharpening grinder. I have all the polishing wheels to finish and more tools that are necessary. Ok maybe not just a little about me, but now my question is will your turning class help me to fulfill my passion even though it is just a hobby? I also want to ask you if you could guide me in finding hands-on learning. Whether live or e-learning I have no interest in learning the skew chisel at this point. The skew chisel terrifies me. Having mentioned the skew chisel, I also got a safety shield leather apron, and safety tools. I now have a replacement faceshield because of the skew chisle.
Glen,
Thank you for writing and sharing!
You are here! I created Turn A Wood Bowl University for YOU…and others like you. 😉 So many of us don’t have access to live teaching, and frankly that doesn’t guarantee success. It all depends on the instructor.
I’ve put together three courses (so far) that cover all the bases, Sharpening, Gathering Green Wood, and the most important Turning! Each course walks you through everything you need to know, without skipping any details! Take a look at this page and be sure to look at the bottom and see what others are saying. https://turnawoodbowl.com/wood-bowl-turning-start-to-finish-online-ecourse/
Oh! And I don’t use the skew chisel at all when making bowls. So, not to worry. 😉
All the best to you and Happy Turning!
Kent, can’t say thank you enough for your outstanding courses and videos. Your layout, camera work and clarity is exceptional . You are a gifted instructor and teacher. I have finished the sharpening (about a dozen times!) and turning courses and I am having so much fun! I am 79 y/o, never used a lathe but decided to give it a go. Bought a used Delta midi, made a bench, put in new bearings, spindle shaft, belt, cleaned and painted it . Came with a lot of used but mostly usable accessories including some mid point turning tools which were kind of used up . My best purchases have been your courses and sharpening system with CBN and a Wolverine set up. The only problem I have encountered was when I “skipped ahead” had some catches and picked up a couple of blanks off the floor,. You taught me what not to do and I have since successfully turned several without problems.
My only area I have to work on more is sharpening but I am getting there. There is nothing as sweet as the first cut with a really sharp gouge.
I leave with 2 questions.:
Are the lower price gouges good quality? While I am still learning I am afraid to grind away at a $150 tool but maybe it is worth it?
And do you ever plan to hold on site training workshops ?
Sign me up if so!
Thanks again,
Gary T
Gary,
Thank you kindly! I’m thrilled you are learning and having fun! Yes, sharp tools are the best.
I would not go to the bottom of the barrel tools out there, but the $150 tools aren’t necessary either. Check out the tools I recommend here http://www.TurnAWoodBowl.com/gear I use all of this gear and the tools are more than fine at a much more reasonable price, especially when starting out.
Unfortunately, I do not have the space to do live training courses. That is why I’m focused on all the online training. Thanks for asking.
All the best to you and Happy Turning!
Kent
Kent, thank you for the work you are doing. I enjoy the courses very much have learned a great deal.
I have had a repeat issue with turning the bottom of the bowl, establishing the tenon and platform for the bowl. The outside is done.
I turn the bowl around and mount to the chuck and the bowl seems to be out of round again. Is this a normal issue? I find it disconcerting and try to true up the bottom again. Any thoughts?
Jim
Jim,
Yes, this is usual.
It’s almost impossible to reverse the bowl and put it on the same exact axis. A little wobble is common. You’ll want to fuss and center it more if it’s really out of true.
Usually, if you shape the foot area, even with a slight off-center mount, it won’t be visible. I merge the two areas with a little focused sanding and all is good.
Happy Turning!
Kent
Thanks, that eases my mind.
Jim
Fantastic! That’s a great outcome! Happy Turning!
Would like to take the course but can’t do PayPal any longer due to liberal controls. Please advise best way to pay you.
Thanks
Blair,
Email me a kw@turnawoodbowl.com and I can send you an address to mail a check if you’d like.
Thank you,
Kent
Kent, good evening! I have a question about turning live edge bowls from round logs vs logs cut in half. I have tried turning 2 live edge bowls from round logs. I ended up turning away two of the sides when I was removing the bowl interior and ended up with only 2 viable sides. I do not have this problem when turning logs that have been cut in half first. I am mounting the round logs the same way I do the other….I have them mounted on their sides, not end to end on the tail stock / head stock. My guess is there is a formula I need to be using….diameter of the log vs. length of the log. I am thinking that the diameter needs to be greater than the length or equal to it. Can you set me on the right path? Thank you sir!
Kind regards,
Trey
Trey,
This is a bit of a 3D puzzle. I will be explaining this more in the upcoming Green Wood Online eCourse. Yes, with a natural or live edge bowl you can turn a diameter larger than the width of the log, but don’t cut down and past the apex of the width. Not sure if that is easily understood? LOL
Happy Turning!
Kent
Kind of understood, thank you. Do you know when your Green Wood Online eCourse is beginning? Looking forward to taking it. If it is half as good as your first two eCourses, it will be awesome and very informative/educational!!
Trey, thank you for the kind words. I’m thinking it will be out in later summer. Stay tuned. Happy Turning!
I can’t thank you enough for this course. It has really help with my confidence and skill. I was able to do the exercises and not have any catches. That gave me the confidence to tackle 2 live edge bowls. Though they are not perfect, they are functional, but best of all there were no issues during the turning process. Thank you, thank you, thank you!!!! You put this together perfectly and I appreciate your quick responses to my questions! Looking forward to the next chapter, and shared your page and encouraged friends that are also new to turning to sign up!! Thank you again!!
Regards
Trey
Trey, Wow! Thank you! I’m so glad you’ve enjoyed the course and are benefitting from your new skills! Enjoy and all the best to you. Happy Turning!
What coring tool do you recommend for turning a segmented wooden bowl of walnut and maple?
Jay Griesser
Hi Kent, i teach members of my local Mens Shed and basically teach them how to use each gouge/chisel, ie roughing gouge, bowl gouge, spindle gouge, parting tool, skew chisel and scraper. As well we make a garden dibber, honey dipper, saucer, bowl, bud vase and candle stick. I run the course over 8 weeks, 2 hours per week. They also get a “lesson” in grain direction, laws of wood turning.
The question i would like to ask is- is this what you would do to get a beginner familiar with woodturning to understand the basics? Or do you have an alternative course that you would recommend?
Thanks, Brian
Hello Brian,
Thanks for writing and good question.
Well, I like to think there are two different main paths in woodturning – spindle and bowl turning.
I focus mainly on bowl turning. However, there are many aspects, like grain direction, etc that are necessary for both.
My course is designed to teach every aspect of turning a bowl and everything you need to do with the bowl gouge to complete that process. Along the way we also cover grain direction and many reasons things work better one way versus another.
A person going through this course will have a very thorough understanding and experience of bowl turning that can be applied to any future turnings.
Hope that answers your question.
Thanks and Happy Turning!
Hello Kent,
Thanks for the safety info.
I’m taking your e-course for turning now.
I have turned 7 of the 14 blanks I made up to lesson # 18 and am wondering what the proper height the spindle should be in relation to my shoulders. It is now 39 inches from the floor and my shoulders are 56 inches from the floor.
I put a 6 inch pallet down and it seemed to be more comfortable. Just wondering if I should make a lower stand or a platform to stand on🤔
Thanks,
Dave
Dave,
Good question.
An ideal height should be around the height of your elbow when you are standing straight. See where your elbow is located on and off the pallet, first. And then go from there.
Hope that helps.
I took your advice and built a custom bench for my comet 14 DR nova lathe. Seems to be working out just great. Thanks.
Fantastic! Enjoy and Happy Turning!
Where is the tool list?
Lesson 4 — Equipment
Thanks Kent,
That’s almost where it is with the pallet.
I’m just starting my 9th bowl removing the centers. I’m using a Pinnacle 1/2″ fingernail grind gouge @ 55 deg. and sharpening with OneWay varigrind system. Having trouble riding the bevel on the inside but not too bad on the external. I tried thinning the heal using your Depth gauge (which works out great).
Dave
Dave, Sounds great. Thanks for sharing!
Hi Kent.
As I go through the coarse, and I make comments, is there any type of indicator on my account to let me know you have responded? Tyvm sir, love this coarse.
Good question. I’m not sure if the system sends an email notification when a comment has been returned. Hm? I’ll see what I can find. In the meantime, I guess checking back on the pages where the comment was posted is the best method of seeing replies.
Kent, Finished the course was worth every penny ! I believe every lathe Maker should buy the course as part of the lathe sale to first time owners.
On another question what tooth spacing do you use on your band saw ? I have a old general bandsaw 2 HP I was going to set it up for strictly cutting my bowl blanks. I was thinking 3 to 4 tooth per inch .
Again thanks for the course it was very helpful to a first time turner.
David,
Thank you for your kind words. I think you might be onto something with that manufacturer’s mandate. Ha! 😉
My bandsaw teeth are 3-4 per inch. If you’re used to finer teeth be careful, these can grab if the wood isn’t stable.
All the best to you and thanks again!
Happy Turning,
Kent
Kent. What are you feelings on a negative rake scraper??? Also I’m considering getting a CBN 180 grit 4-in-1 wheel. I would love your thoughts on this.
George ( Freddy McKenna) McLean
Thanks, George, take a look at this video where I cover the negative rake scraper. https://youtu.be/1k3Fpfs_Cms I think the 4in1 wheel is a bit pricey and I have a wheel with rounded edges and it seems easier to run the tool off the edge of that wheel. I’d stick with the ones I have listed in my Recommended Equipment page here > https://turnawoodbowl.com/recommended-equipment/recommended-sharpening-equipment-2/ Happy Turning!
Thanks Kent. I thought that wheel was a bit pricy as well. I just purchased your sharping E course. In for a penny in for a pound!!
I’ve now gone back to the beginning of your turn a bowl course and glued up 6 blanks. It will be nice to have nice sharp tools.
Do you think a CBN wheel is worth it?
George,
Sharp tools are critical.
Yes, the CBN wheels are a lifetime purchase and do an excellent job sharpening tools compared to oxide wheels.
Happy Turning,
Kent
Hi Kent – I love your videos and I’m keen to get started up on your course so I can make the transition from carbide to bowl gouge. I know the course may be extended and modified from time to time, but what is the rough estimate of instructional time across all of the various videos at present? Thanks!
Jeff,
Thank you for writing and inquiring. If you are eager, you can watch all the lessons in this Course in one day. But I recommend taking your time and progressing through the material as you practice the skills in each lesson. I would say, if you are uninterrupted you can complete the course and do all the exerices, which will result in several completed small bowls, within one week’s time.
Thanks for asking, and we’ll see you in the Course soon. Enjoy!
Happy Turning,
Kent
Hello Kent, I am truly enjoying the bowl course , Just wanted to pass on a tip a Bowl Turner and neighbor showed me. About the tool rest height. What he explained to me is to run the tool rest up to the head stock or the tail stock set the height, then move the tool rest to the side of the head stock and place a piece of tape there and mark the height. this way you can just slide the rest over to the mark and you then know the center height then just drop whatever is required . Again really enjoying the course.
Dave L
David,
Thanks for sharing. Keep in mind, this works if you have one tool and use it in roughly the same orientation each time. A larger or smaller bowl gouge will require the tool rest to be raised or lowered accordingly.
Happy Turning,
Kent
Hello Kent, I am up in Northern NH and it is a two hour drive for me to go to a lumber retailer that would sell bowl blanks Wood Craft Etc. I do however have a sawmill and can cut anything I would like for a bowl blank from the Northern Hardwoods. This means I would be turning green, for the object of this class would this make a difference if I turned say White Birch, Popular, or Cherry ? I would like to know this prior to signing up for the class.
Thanks Dave Landry
Dave,
What a great resource you have!
No, this will not effect the course for you at all. Just cut blanks similar in size to the ones we will be making.
Any species will do, as I will be demonstrating cutting techniques that will cut any density of wood, as long as the bowl gouge is sharp.
Thanks for sharing and I look forward to having you in this Course.
Happy Turning,
Kent
I have a lathe and the 3 carbide tools (roughing, finisher & detailer) as well as a homemade thin parting tool. I will be buying a bowl gouge after Christmas, what other tools are necessary to get the most out of this course.
Ray,
Great question.
A 1/2″ bowl gouge and a sharpening system are the main elements. You will need a tenon scraping tool which can be a scraper or a detail spindle gouge. Also, you will need a way to initially attach the bowl blank to the lathe (faceplate, spur drive, screw chuck – we’ll cover all of these) and a four-jaw chuck to reverse the bowl on the lathe. That’s about all
See you in the course.
Happy Turning,
Kent
Wow, I didn’t realize that I need to buy a gouge, a grinder and a sharpening system as well as a chuck + the cost of the course. Do you offer a version of the course using just carbide tools, this would mean that I only need to buy the chuck. I’m sure that I am not the only newbie that wants to learn bowl turning while staying on a budget. Carbide tools were cheap as I just bought the cutters and a length of 1/2 steel and made my own.
Good question. You can follow all the lessons in this course and substitute carbide tools if you’d like. Some bowl gouge lessons obviously won’t apply, but all the turning aspects are the same. Thanks for asking.
Kent, Dave here was looking into both of your courses, I have my lathe my tools but I have always used a tormak for my sharpening will you be covering this in your class also?
David,
I currently do not have the Tormak covered in this course. In general, there are many aspects of sharpening that you will still gain from this course. I hope to add the tormak system to this course in the future.
Happy Turning,
Kent
Hi Kent,
I want to clarify a few things about your course pricing, you had said that if you join now you will receive a lifetime membership. Does this mean free access to all your videos? I s the price $ US 99. Will this include videos on sharpening too?
Will I receive a login to your site once I’m a lifetime member?
Hello Danny,
Thanks for the question.
Each course is separate, but I do cover sharpening the 1/2″ 55° bevel swept-back bowl gouge in my Wood Bowl Turning Start-to-Finish Course. The Tool Sharpening Course thoroughly covers all aspects of shaping and sharpening all tools needed to turn bowls. The two courses are separate.
Yes, once you join a course you will have access to all lessons and videos in those lessons from now on.
You will use your email address as your user name and then create a password to log in to the course whenever you like.
Thanks for the question and I hope to see you in one or both courses soon.
All the best to you and Happy Turning,
Kent
Hi Kent,
I watch a lot of your videos. I thank you for being the best teacher I have engaged on youtube.
I thank you for being so professional , so honest and so dedicated to teach people like me.
I’m trying very hard to teach myself wood turning. Something I never done before !
I love it.
I do absorb a lot more from your videoes than enyone else.
I thank you sincerely, wishing you the best Xmas ever and God’s blessings everyday.
Ben.
Hi Kent,
I watch a lot of your videos. I thank you for being the best teacher I have engaged in youtube.
I thank you for being so professional , so honest and so dedicated to teach people like me.
I’m trying very hard to teach myself wood turning. Something I never done before !
I do absorb a lot more from your videoes than enyone else.
I thank you sincerely, wishing you the best Xmas ever and God’s blessings everyday.
Ben,
Thank you so much for writing and sharing your kind words.
I’m thrilled to help you as you progress along this path.
Be sure to take a look at my new Turning Online Course, it is perfectly suited to guide you through every step of the process.
Check it out here https://turnawoodbowl.com/wood-bowl-turning-start-to-finish-online-ecourse/
All the best to you and Merry Christmas!
Happy Turning,
Kent
Hello kent, was wondering do you have a one time combined price for all your courses. i feel it would be better to join one time for all you courses as i really learn and enjoy them.
thank you
Tim Cook
Tim,
Thanks for asking. I don’t have a combo price at this point. The cost of each course is currently reduced much lower than its full price.
Thanks for asking and Happy Turning,
Kent
Hi Kent,
I’m looking forward to taking your course soon. To follow-up on a question from above about the course material being different from your excellent “free” videos on your YouTube channel–
Will the course videos be the same videos from the channel, just organized better and/or differently, or, new videos dedicated to course content, or both? The most challenging thing about being a newbie is trying to figure out what-to-watch-first on any YouTube channel dedicated to woodworking or turning. It’s pretty overwhelming!
Your channel and content is amazing. Looking forward!
Aaron
Hi Aaron,
The Wood Bowl Turning eCourse videos are all uniquely designed and produced for the course only and do not appear anywhere else.
You will no longer have to hunt around online for which video to watch next. The course videos are all organized in the exact pattern you will need to execute a bowl. Hence the name Wood Bowl Turning Start-to-Finish!
Great question, I look forward to having you in the course soon!
Happy Turning,
Kent
Ken this is Ed I asked the question about the gouges I went back in the lessons and sure enough I found my answer all the info so far is here you just have to go back to find it thank for this course
Hi Kent hope thanksgiving went well for you and your family I have my first practice bowl ready to go my question is I have 3 gouges 1/4, 1/2 and 3/4 inches which on should I use to get going
Any of them will do, but the 1/2″ is the one I’ll be using throughout this course. Thank you.
Kent,
Are you going to cover live edge bowls in this course as well as the traditional finished bowls?
Brad,
Good question. This course is designed to teach the fundamentals of wood bowl turning. I may cover live edge turning in a different course. We are focused on getting all the steps, techniques, and skills established to make wood bowls in this course. Thanks and I hope to see you here soon.
Happy Turning,
Kent
Will all courses be videoed or will some be live demonstrations?
Dean,
All the lessons are in video form and saved to each page so you can come back to them as much as you need, as often as you like, and whenever you need.
Hello, question is what kind of screws do I need to use to mount faceplate to a blank? Great courses. Watch your video on tube
Cecil
Cecil,
I recommend Robertson screws (square headed) and an impact driver is ideal. Regular drills can easily strip the screws, but impact drivers easily drive and pull the screws. I hope that helps.
All the best to you and Happy Turning!
Kent
Hey Kent!
When we sign up for this course will we have access to the content for only a certain period of time? Or is it always available after purchase? If this is stated somewhere already, my apologies for asking a redundant question.
Bruce
Bruce,
Good quesiton.
When you sign up, you have LIFETIME ACCESS whenever you’d like.
See you in the course.
Happy Turning,
Kent
Kent does the sharpening section of this course contain all the info contained in you sharpening e-course or will I have to take that one also.
Tom,
Thanks for the question. No, the Tool Sharpening Course is separate and independent of the turning course. We will briefly cover how to sharpening the bowl gouge used in the turning course, but the sharpening course covers all tools used when turning wood bowls plus much more.
Thanks,
Kent
Kent, including instructions for those
Good morning. I have previously asked if you would consider video courses for those of us who use carbide turning tools for the entire project. I have not received an answer to date.
Chris,
In this online eCourse, I will be helping beginners, those who have started turning bowls, and carbide turners learn to turn with traditional woodturning tools, especially the bowl gouge. I may do a video about carbide turning in the future, but traditional tools render the best results when turning bowls.
Thanks and Happy Turning,
Kent
How will this differ from all the great information you already provide free?
Great question. This online eCourse is methodically laid out so you can follow the entire process of bowl turning from start to finish and see all the details (and options) along the way. You will learn the “process” most effectively by seeing and doing. We have exercises at various points along the way to reinforce the lessons. Also, the lessons are organized, easy to find, and always available for you to view. Learning in this manner will greatly accelerate your skills and help you along your journey to make the bowls you imagine. I hope to see you in the Course soon. Happy Turning!
I like the sound of this course. One problem. Living in the U.K. !I have had problems
buying equipment from the U.S.A on several occasions my order has apparently been ignored. will this happen again should I place an order for one of these courses, or will I be wasting my time?
Hello Ernie,
I’m sorry to hear you had orders ignored by others.
No, I will not ignore your order when you sign up for this Course.
This course is delivered online and you will have access as soon as you sign up.
Thanks for writing!
Happy Turning,
Kent